- Homepage
- News
- Blogs & Articles
- FIA Tour of Manufacturing Technology Centre (MTC)
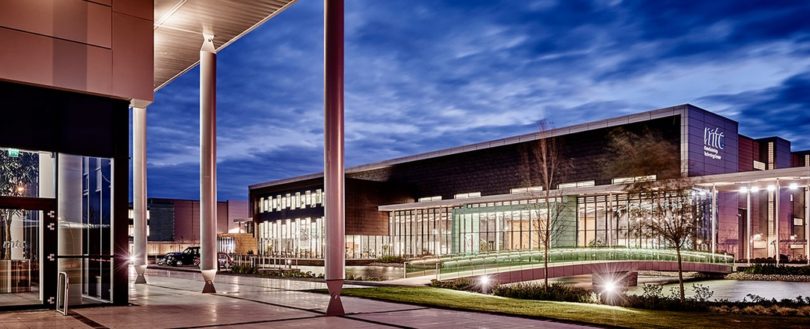
FIA Tour of Manufacturing Technology Centre (MTC)
Like it? Share it!
A lovely sunny day was ideal to show off the spacious campus of the Manufacturing Technology Centre, Coventry. One building houses a conference centre and training facility and is separated by an ornamental pond and a connecting bridge to the advanced manufacturing demonstration building. About 30 FIA members had gathered today, all eager to learn about the work of this new facility. Derek Gotts, welcomed members and introduced Nigel Knapp, Business Development Manager at the MTC. Nigel proudly described the resources available and the work of the MTC. Established in 2010 the mission is to bridge the gap between academic research and industry. This gap is referred to as the valley of death because many good ideas formed through UK research are failing to materialise in UK manufacturing. Instead often these ideas are being implemented by overseas companies. Government identified this area was in need of support and the MTC is the result of a £450m investment to bridge this gap.
The MTC is part of a network of facilities spread across the UK and this centre focuses on High Value Manufacturing Catapult to encourage future growth in industry. The organisation works with all sizes of business but the focus of the FIA members was on the support for SMEs. The MTC is able to provide support and R&D to develop products from the stage of advanced prototype through to implementation of new technology in the manufacture of the first 100 prototypes.
Their expertise can be applied to an item that has never previously been made or assembled and will particularly help companies in three areas:
• Addressing manufacturing needs to reduce cost, improve quality, faster and at higher volume
• Assemble a product or component at lower cost, improved quality faster or at higher volume
• Use data more effectively to improve design, improve quality and logistics, or to implement a new business model.
Through the SME REACH scheme, the MTC is able to help companies embed innovation and de-risk the use of technology. This scheme is able to subsidise 50% of the cost of up to 30 days use of the research centre and is able to develop products through their Product Manufacturing Incubator.
Following the presentation in the training centre we crossed the bridge to visit the demonstration manufacturing facility. Spread over the extensive manufacturing floor were some of the most advanced tools and machines able to create components as large and complex as an aircraft wing down to tiny components for a medical implant. The machines focused on robotic assembly, welding and Net Shape & Additive Manufacturing Solutions. Some incredible sample products were available to demonstrate the capabilities of these machines to improve the manufacturer of either the product itself, or the tools that will be used to make a product.
When the tour was over, we returned to the training centre for a de-brief, coffee, biscuits and an opportunity to discuss the exciting ideas that we had seen. Several members were encouraged to sign up for more information and ideas were stimulated for further discussion.
9th March 2017
Related posts
-
Fireside Chat with Managing Director and Founder of RayFire Services Ltd, Ray Hope
25 March 2024
By Charlotte Brill, Content Marketing Executive
-
Gateways 2 and 3 - What will be the impact on fire safety engineers?
08 January 2024
By Jon Pagan, Head of Technical at Kiwa Fire Safety Compliance & FIA Fire Engineering Council Chair
-
Ensuring fire safety in schools: responsibilities, developments, and training
06 October 2023
By Neil Budd, FIA Technical manager
Related news
-
FIA Launches BS 5839-1:2025 Guidance Note
20 June 2025